
The scalability is the major issue in the current on-line condition monitoring applications. During those initial stages of online condition monitoring, the accessibility of such applications was through personal computers and laptops via World Wide Web.
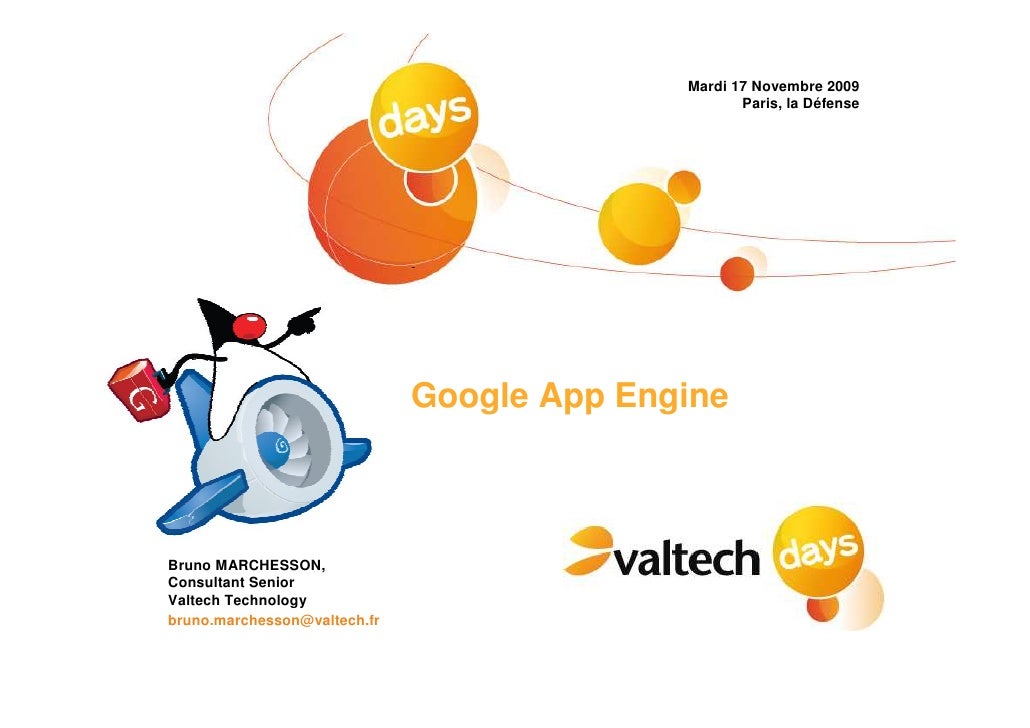
This methodology leads to better preventive maintenance, but predictive maintenance is still a challenge. In the late 90’s, very few online condition monitoring applications came into existence with the primary motive to collect vibration signals from various machines operating at different locations, but the analysis has been made considering each local operating environment to make effective decisions. The major challenge faced by many industries is not only inadequate storage space but also the scalability when many machines inside the plant or operating at remote locations are to be monitored online and enormous amount of data have to be acquired from the machines for the interpretation of their behaviour at dynamic or abnormal operating conditions. The current condition monitoring systems make effective decisions using the knowledge repository, which is populated using various algorithms by the way of observing and storing the defective and unusual behaviour details of the machines. The uptime and efficiency of the plant operations shall be maximized through proper condition monitoring diagnostics and as well as preventive or predictive maintenance. Condition monitoring is heading as a real-time task, which requires maximum accuracy and embraces a gradual paradigm shift from legacy systems to modern Internet of Things (IoT) enabled systems at every level namely data acquisition, data processing, data integration and decision making. Condition monitoring of electrical machines is extremely significant for making the industrial processes more efficient with reduced downtime. The electrical machines find wide and crucial applications in various industries and power plants. The resulting threshold values are compared with that of the vibration analysis carried out on the machine beds locally using myRIO for data acquisition in LabVIEW and the proposed model ensures the integrity in appropriate decision making with assured scalability. The deployed cloud service for the enhanced statistical classification algorithm eliminates the false identification of failures, which not only increase the availability of machines for intended operations but also reduce the maintenance cost. The services have been deployed without any limitation in a cloud environment and the industrial applications can share information using the deployed services from anywhere on demand basis. The computational engine will do inherent statistical analysis of the vibration signals to estimate the cluster of thresholds adaptive to various operating conditions.
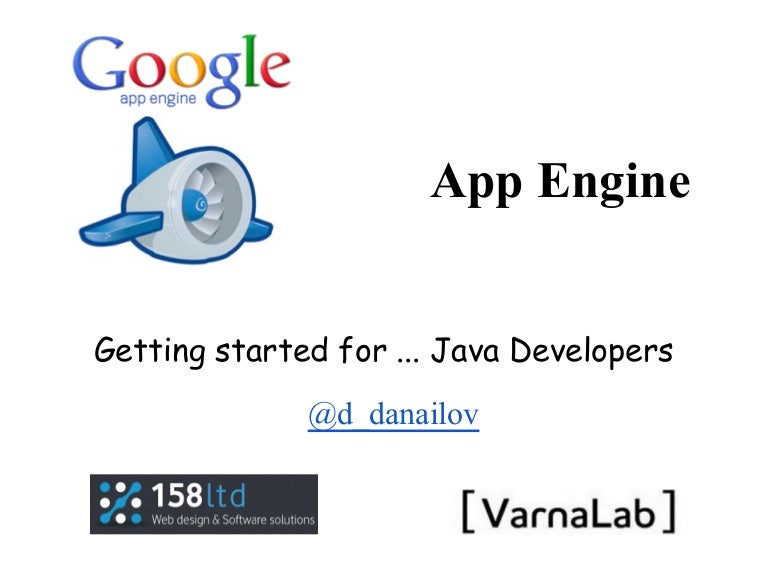
This cloud-based vibration monitoring model provides services for data acquisition from the IoT devices mounted on the shafts of the DC motors, data storage to store the enormous amount of acquired signal data from multiple sensors, data classification of vibration signals for effective statistical analysis to estimate adaptive cluster of thresholds and appropriate decision-making services on demand over the Internet to utilize the reliable service of the machines in a persistent way.
#Google app engine sdk 1.9.27 generator#
An experimental setup consisting of two DC motors coupled to AC Generator operating at different locations is considered to evolve the proposed model for effective integrated monitoring and decision making.
#Google app engine sdk 1.9.27 software#
The proposed Software as a Service, Storage as a Service and Platform as a Service layers address the challenges of data storage and scalability while making analysis on the cluster of machines in an Industrial Environment. Cloud services are proposed for real-time data acquisition, data classification, data processing and decision making, which are highly interconnected services for effective condition monitoring of electrical machines.
